HOME
/
The Secrets Of 5 Scenarios Where Stainless Steel Cable Ties Shine
The Secrets Of 5 Scenarios Where Stainless Steel Cable Ties Shine
Stainless steel cable ties are robust fastening devices made from corrosion-resistant stainless steel. They are designed to securely bundle and organize cables, wires, hoses, and other components in various industrial and commercial settings. Unlike traditional plastic ties, stainless steel cable ties offer exceptional durability and strength, making them suitable for demanding environments.
Stainless steel cable ties play a crucial role across a wide range of applications due to their superior qualities. They provide secure and reliable fastening in industries such as aerospace, automotive, marine, electrical, and telecommunications. Their ability to withstand harsh conditions, including corrosion, high temperatures, and mechanical stress, makes them indispensable for ensuring safety, reliability, and efficiency in diverse operational environments.
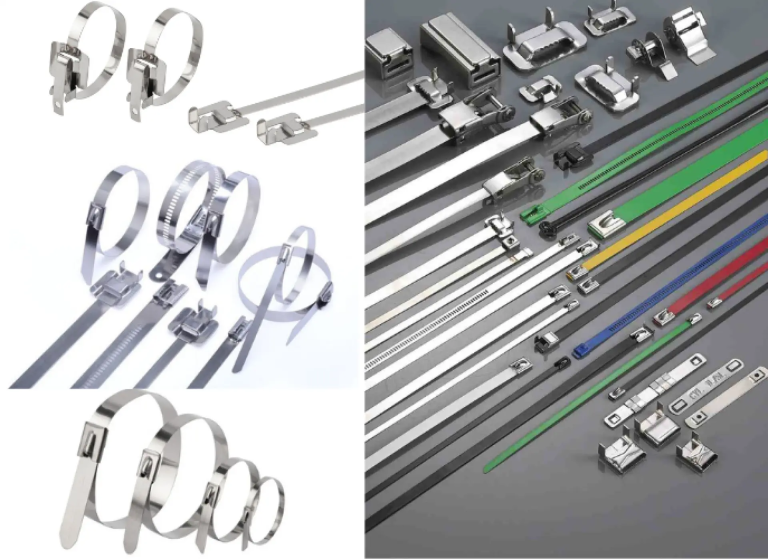
What makes stainless steel cable ties different?
1. Material Composition of Stainless Steel Cable Ties
Stainless steel cable ties are made primarily from stainless steel, an alloy known for its exceptional properties. This alloy typically contains a mix of iron, chromium, nickel, and other elements, which contribute to its strength, durability, and resistance to corrosion. The chromium content, usually around 10.5% or more, forms a passive layer of chromium oxide on the surface, which protects the steel from rust and other types of corrosion. Nickel, on the other hand, enhances the overall toughness and resistance to oxidation, making stainless steel cable ties robust and reliable in various applications. These ties are often manufactured from specific grades of stainless steel, such as 304 or 316, which offer distinct levels of resistance to different environmental conditions.
2. Benefits of Strength and Durability in Challenging Environments
The strength and durability of stainless steel cable ties make them indispensable in demanding environments. Unlike their plastic counterparts, stainless steel ties can withstand extreme temperatures, from the freezing cold to intense heat, without losing their structural integrity. This makes them ideal for use in outdoor applications where they are exposed to harsh weather conditions. Additionally, their high tensile strength ensures that they can securely hold heavy cables and components without snapping or loosening. The durability of stainless steel cable ties means they have a longer lifespan, reducing the need for frequent replacements and maintenance, which is particularly beneficial in industrial and marine settings where reliability is paramount.
3. Properties of Stainless Steel That Resist Corrosion
Stainless steel’s most notable property is its ability to resist corrosion, which is primarily due to its chromium content. When exposed to oxygen, chromium forms a thin, stable layer of chromium oxide on the surface of the steel. This layer acts as a barrier, preventing further oxidation and protecting the underlying metal from rust and other forms of corrosion. This self-repairing quality of stainless steel ensures that even if the surface is scratched or damaged, the protective oxide layer will reform. Moreover, stainless steel’s resistance to chemicals and acids makes it suitable for use in environments where exposure to corrosive substances is a concern, such as chemical plants, food processing facilities, and coastal areas.

4. Applications in Corrosive Environments
Stainless steel cable ties are widely used in environments where corrosion resistance is crucial. In marine environments, where saltwater and humid conditions can rapidly degrade other materials, stainless steel ties provide reliable performance. They are commonly used to secure cables and components on ships, offshore oil rigs, and coastal installations. In industrial settings, stainless steel cable ties are employed in chemical plants and refineries where exposure to corrosive chemicals and high temperatures is a constant challenge. They are also used in the construction of infrastructure in coastal areas, where the air contains high levels of salt that can accelerate corrosion. Additionally, in the food processing and pharmaceutical industries, stainless steel’s resistance to organic and inorganic chemicals ensures that cable ties remain intact and functional in sanitary environments, where stringent hygiene standards are maintained.
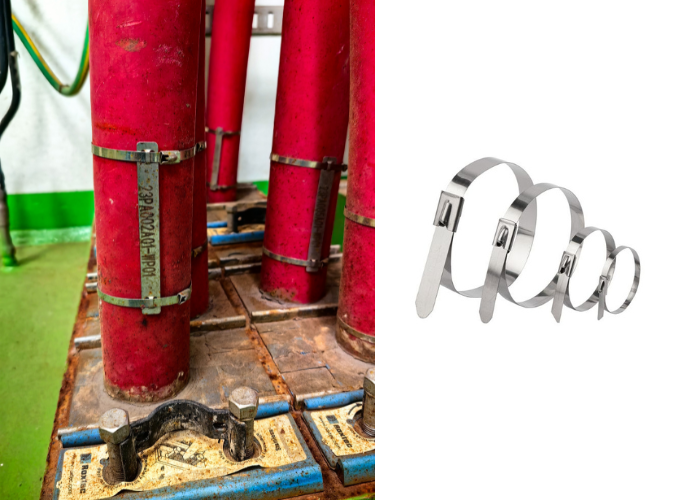
5 Scenarios Where Stainless Steel Cable Ties Shine
1. High-Temperature Applications
Ability to Withstand Heat and Extreme Temperatures
Stainless steel cable ties are specifically designed to perform exceptionally well in high-temperature environments. The alloy’s composition, particularly the presence of chromium and nickel, allows it to maintain its structural integrity and mechanical properties even when exposed to extreme temperatures. These cable ties can withstand temperatures ranging from sub-zero levels to as high as 1000°F (537°C) or more, depending on the specific grade of stainless steel used. The heat resistance of stainless steel prevents deformation, melting, or degradation, ensuring that the cable ties remain secure and functional in applications where other materials would fail. This makes stainless steel cable ties an ideal choice for environments subject to significant thermal fluctuations and high-heat conditions.
Examples of Industries Where High-Temperature Resistance is Critical
* Aerospace Industry: In the aerospace industry, components are often exposed to extreme temperatures during flight and in various atmospheric conditions. Stainless steel cable ties are used to secure cables and components within aircraft, ensuring reliability and safety under these demanding conditions. The heat resistance of stainless steel is crucial for maintaining the integrity of these components during flight.
* Automotive Industry: In automotive manufacturing, particularly in engine compartments and exhaust systems, components can be exposed to very high temperatures. Stainless steel cable ties are utilized to secure wiring harnesses and other critical components, ensuring they remain intact and functional despite the intense heat generated by the engine and exhaust.
* Oil and Gas Industry: The oil and gas industry often involves operations in harsh and high-temperature environments, such as drilling and refining processes. Stainless steel cable ties are used to secure cables and equipment in these settings, where they must withstand not only high temperatures but also exposure to corrosive substances and mechanical stress.
* Power Generation: Power plants, especially those using fossil fuels or nuclear energy, operate at high temperatures to generate electricity. Stainless steel cable ties are employed to manage and secure cables and components within these plants, ensuring continuous operation and safety in high-heat environments.
* Industrial Manufacturing: Many manufacturing processes, such as metal forging, glass production, and chemical processing, involve extreme temperatures. Stainless steel cable ties are used to secure machinery, cables, and other components that are subjected to these high-temperature conditions, ensuring stability and durability.
Stainless steel cable ties offer unparalleled performance in high-temperature applications due to their exceptional heat resistance and durability. Their use in industries like aerospace, automotive, oil and gas, power generation, and industrial manufacturing highlights their critical role in ensuring safety, reliability, and longevity in environments where other materials would fail.
2. Outdoor and Harsh Environments
Protection Against Weather Elements and UV Exposure
Stainless steel cable ties provide excellent protection against various weather elements and UV exposure, making them ideal for outdoor and harsh environments. Unlike plastic ties, which can degrade and become brittle when exposed to sunlight, stainless steel ties are inherently resistant to UV radiation. This resistance ensures that they maintain their strength and flexibility even after prolonged exposure to the sun. Additionally, stainless steel ties are impervious to rain, snow, ice, and extreme temperatures, preventing rust, corrosion, and weakening. Their ability to withstand these conditions makes them reliable for long-term use in outdoor applications where constant exposure to the elements is unavoidable.
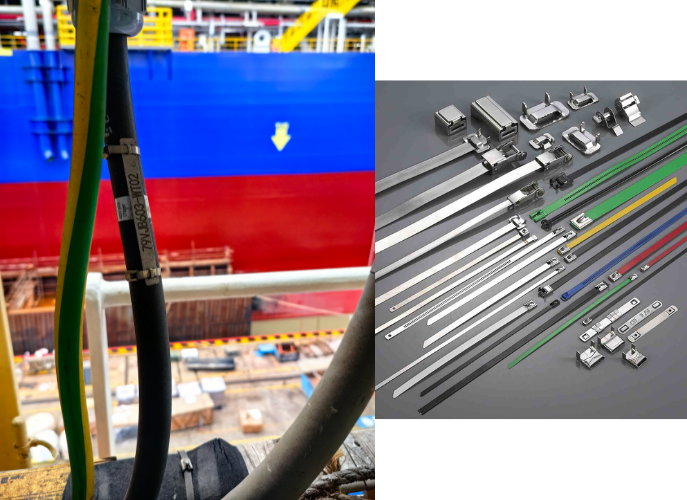
Use in Outdoor Installations and Industrial Settings
Stainless steel cable ties are extensively used in outdoor installations and industrial settings due to their robust performance and durability. In outdoor installations, such as securing fencing, signage, and lighting fixtures, these ties ensure that components remain securely fastened, regardless of weather conditions. They are also used in telecommunication and electrical installations, where cables and equipment need to be held in place in environments exposed to wind, rain, and UV light.
In industrial settings, stainless steel cable ties are employed in construction projects, mining operations, and oil and gas facilities, where they must endure harsh conditions and mechanical stress. Their resistance to chemicals, moisture, and temperature fluctuations ensures that they can handle the demanding environments found in these industries. For example, in construction, they are used to secure scaffolding, pipelines, and structural elements, while in mining, they hold cables and equipment in place amidst abrasive conditions. In the oil and gas sector, stainless steel cable ties are critical for securing components in refineries and offshore platforms, where exposure to saltwater and corrosive substances is a constant challenge.
3. Electrical and Electronic Applications
Insulation and Grounding Properties
Stainless steel cable ties play a crucial role in electrical and electronic applications due to their unique properties. While stainless steel itself is a conductor, these cable ties can be coated or used in conjunction with insulating materials to prevent electrical conduction where needed. In scenarios where grounding is essential, uncoated stainless steel ties can serve to securely ground electrical components, ensuring safety and compliance with electrical standards. The combination of their strength and potential for customization with insulating coatings makes them versatile tools for managing electrical systems, preventing short circuits, and maintaining electrical integrity.
Applications in Securing Cables and Components
In electrical and electronic applications, the primary use of stainless steel cable ties is to secure cables and components effectively. They are widely used in wiring harnesses, electrical panels, and server racks to keep cables organized and in place. Their high tensile strength ensures that even heavy bundles of cables remain securely fastened, reducing the risk of cable damage and improving the overall reliability of the electrical system.
In industrial and commercial settings, stainless steel cable ties are essential for securing large electrical cables that carry significant current loads. Their durability ensures they can withstand the vibrations and physical stresses often encountered in these environments. Additionally, in electronic devices and equipment, stainless steel cable ties help manage internal wiring, preventing tangling and maintaining the integrity of connections.
Stainless steel cable ties are also used in outdoor electrical installations, such as power lines and communication networks, where exposure to weather elements and UV radiation is a concern. Their resistance to corrosion and environmental degradation makes them ideal for these applications, ensuring long-term performance and reliability.

4. Automotive and Aerospace Uses
Securing Components in Vehicles and Aircraft
Stainless steel cable ties are extensively used in both the automotive and aerospace industries for securing various components within vehicles and aircraft. In the automotive sector, these ties are employed to manage and secure wiring harnesses, brake lines, fuel lines, and other critical systems. Their ability to withstand high temperatures and resist corrosion makes them ideal for use in engine compartments, exhaust systems, and undercarriages, where they are exposed to extreme heat, oil, chemicals, and road debris.
In the aerospace industry, stainless steel cable ties are crucial for securing cables, hoses, and other components in aircraft. Given the rigorous safety standards and the extreme conditions faced during flight, these ties must be able to endure significant stress, vibrations, and temperature variations without failing. They are used in various parts of the aircraft, including the fuselage, wings, and engine compartments, ensuring that all critical systems remain securely fastened throughout the aircraft’s lifespan.
Benefits in Terms of Safety and Reliability
The use of stainless steel cable ties in the automotive and aerospace industries provides significant benefits in terms of safety and reliability. Their high tensile strength ensures that they can securely hold heavy cables and components, preventing movement and potential damage that could lead to system failures. This is particularly important in vehicles and aircraft, where the integrity of all systems is critical for safe operation.
The durability and resistance to environmental factors offered by stainless steel cable ties contribute to their reliability. In the automotive industry, their ability to withstand harsh conditions, such as exposure to road salt, oil, and extreme temperatures, ensures that they remain effective over the vehicle’s lifespan. This reduces the need for frequent maintenance and replacements, enhancing overall vehicle reliability.
In aerospace applications, the reliability of stainless steel cable ties is paramount. Their resistance to high temperatures and vibration ensures that all components remain securely fastened during flight, reducing the risk of electrical failures, leaks, or other malfunctions that could compromise the safety of the aircraft and its occupants. The consistent performance of these cable ties under extreme conditions contributes to the overall safety and dependability of aircraft systems.
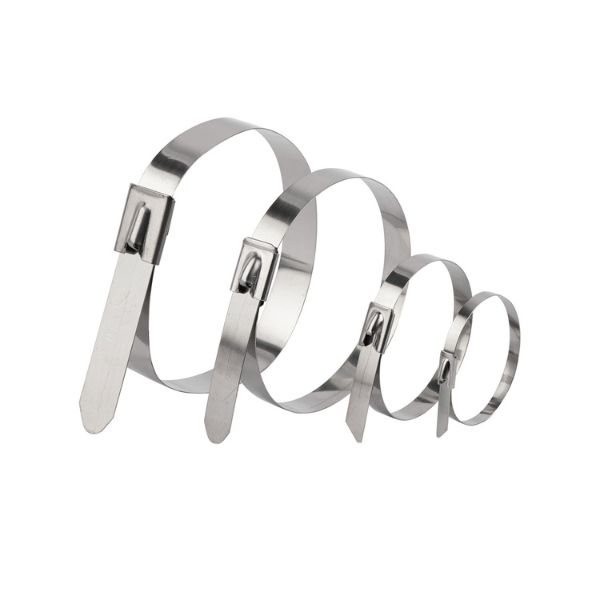
5. Specialized Industries
Marine Applications and Saltwater Resistance
Stainless steel cable ties are exceptionally suited for marine applications due to their outstanding resistance to saltwater and corrosive environments. In marine settings, such as on ships, boats, offshore oil rigs, and coastal installations, the constant exposure to saltwater can rapidly corrode and weaken most materials. However, stainless steel, particularly grades like 316, contains molybdenum, which enhances its corrosion resistance and makes it particularly effective against the harsh conditions found in marine environments.
These cable ties are used to secure ropes, cables, and other components on deck, in the engine room, and in various marine equipment. Their durability ensures that they can withstand the mechanical stresses and corrosive effects of saltwater, maintaining the integrity of marine operations. This reliability reduces the risk of equipment failure and enhances the safety of maritime activities, whether they involve transportation, fishing, or oil extraction.
Medical and Food Processing Industries
In the medical and food processing industries, stainless steel cable ties are valued for their hygienic properties, corrosion resistance, and ability to withstand frequent cleaning and sterilization processes. In medical environments, where maintaining sterility is crucial, stainless steel ties are used to secure medical equipment, organize cables, and fasten components in operating rooms and laboratories. Their resistance to harsh disinfectants and high-temperature sterilization methods ensures they remain effective without degrading or contaminating sterile environments.
Similarly, in the food processing industry, stainless steel cable ties are used to secure machinery, organize cables, and fasten components in processing plants. The stringent hygiene standards in this industry require materials that can withstand exposure to water, cleaning agents, and various chemicals without corroding or compromising food safety. Stainless steel ties meet these requirements, ensuring that equipment remains secure and operational while maintaining compliance with health and safety regulations.
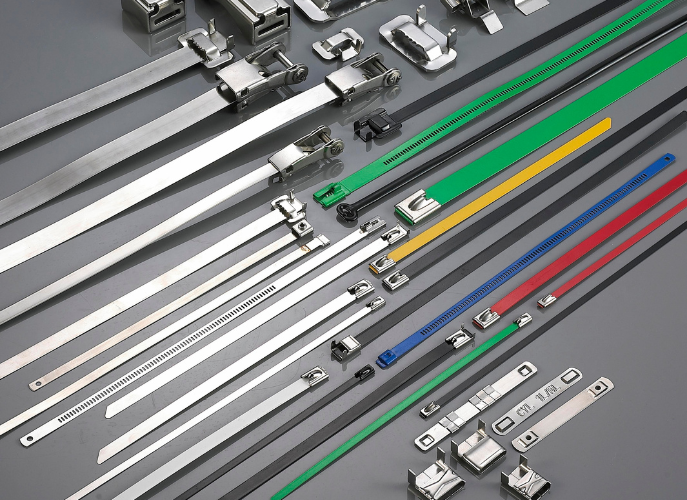
Conclusion
Stainless steel cable ties offer numerous benefits that make them essential across various industries. Their composition of iron, chromium, and nickel provides exceptional strength, durability, and corrosion resistance, allowing them to withstand harsh environments and extreme temperatures. Unlike plastic ties, stainless steel ties do not degrade under UV exposure and weather elements, ensuring long-term reliability in outdoor installations. Their high tensile strength makes them capable of securing heavy cables and components, enhancing safety and reducing maintenance needs. Additionally, their hygienic properties and resistance to chemicals make them suitable for specialized applications in medical, food processing, and marine environments.
The future of stainless steel cable ties lies in continuous advancements and innovations. Enhanced alloy compositions could provide even greater resistance to extreme conditions and mechanical stress. The integration of smart technologies, such as sensors and RFID, could enable real-time monitoring of environmental conditions and tie integrity. Sustainable manufacturing processes are likely to reduce the environmental impact of production. Customization with advanced coatings could expand their functionality, providing better insulation or chemical resistance. As industries evolve, tailored solutions for sectors like renewable energy and advanced electronics will drive further innovation, ensuring that stainless steel cable ties remain a critical component in modern applications.